By Michael Vogt, CGCS, CGIA
No other area on the golf course property is as liability sensitive and environmentally worthy of proper planning and scrutiny as the area where golf course chemicals and fertilizers are stored, mixed and loaded for application to the turf. Knowledgeable and expert design in relation to size, space and components will safeguard workers, members and the environment against the event of an unintended chemical release.
Inadequately stored pesticides and improper chemical mixing and loading practices can present a potential risk to co-worker health and to environment. The quality of surface water, groundwater, soil and air can be damaged in areas where pesticides are stored under inappropriate conditions, improperly mixed and loaded into application tanks and where equipment are washed and rinsed after application. Uncontrolled releases or leakages may have serious health and environmental consequences.
The purpose of this document is to provide guidance to golf course superintendents looking for information on appropriate techniques and approaches for the mixing, loading and storage of pesticides. These guidelines were prepared with input from written resources, individuals and organizations with a broad range of expertise and experience. It is a compilation of the best information available regarding the mixing, loading and storage of pesticides. The result is a set of guidelines which represents a general consensus on how pesticide mixing, loading and storage issues should be approached. It is important to remember that mixing, loading and storage needs will vary greatly from golf course to golf course and site to site. No document could specify exactly what approach should be taken in each situation. As such, it should be kept in mind that this document is intended as general guideline only. These are recommendations, not standards or regulations and as such can and should be adjusted to meet individual golf course needs. These recommendations are designed to assist golf course superintendents in managing, renovating and building their storage areas and conduct their mixing and loading operations in ways that will help minimize exposure to pesticides and reduce the risks to public health and the environment. These are not intended to be regulations of any federal, state or local regulatory agency.
The safest approach to any pesticide storage plan is to limit the amounts and types of pesticides stored. The amounts and types of pesticides stored should be maintained at the level that is immediately required and should not be stored beyond short-term needs.
Selecting a Storage Location
An existing or proposed area should be carefully evaluated to determine its suitability for pesticide handling and storage. In particular the potential harm to human health and the environment due to spills, contaminated runoff or fires should be assessed. If possible, the area should be located at least four hundred feet from any public or private drinking water supplies and two hundred from surface water. Separation from water resources should be greater in areas of sandy, rocky or light textured, rapidly draining soils. Whenever feasible, the area should not be located in a 100 year floodplain. Runoff from adjacent areas resulting from a 25 year 24 hour storm (2.9 - 3.6 inches of rainfall) should be diverted around the facility. The site location should be accessible in the event of a fire or any another emergency situation. The pesticide storage area should be protected against direct sunlight, freezing temperatures and extreme heat. Temperatures in the storage area should be kept between 40F and 100F. Pesticides should not be stored outdoors. Where practical, the mixing/loading area should be located in close proximity to or physically attached to the chemical storage facility to minimize the distance that chemicals are transported to combine finished spray mixes. Consideration should also be given to the additional area required by a mixing/loading pad when selecting the site for pesticide storage.
Storage Practices
Pesticide storage should be restricted to a first story room or area which has direct access to the outside. Pesticides should never be stored in basements. Pesticides should be stored in accordance with their label requirements in their original container with the original label attached and clearly visible. They should always be kept off the ground to prevent the accumulation of water in or under the containers. Separation of pesticides by hazard and function is essential. Flammable pesticides should be stored separately from non-flammable pesticides, preferable in a fire proof cabinet. Dry pesticides should be stored above and separately from liquid pesticides to avoid wetting from spills. Fungicides, herbicides and insecticides should be stored in separate locations of the storage area to prevent cross contamination and accidental misuse. Pesticides should be stored away from fertilizer, potable water supplies, seeds and personal protective equipment (PPE) to avoid cross-contamination. Particular care should be taken when storing petroleum based emulsifiable concentrate chemicals due to their potential high volatility. Pesticides should not be stored in the same place as ammonium nitrate fertilizer. Exposure to sunlight can cause pesticides to chemically breakdown. Windows are not recommended in pesticide storage areas do to light infiltration / chemical degradation and security reasons. Because shelf life is difficult to predict, pesticides should not be stored longer than two years.
Two options for storing pesticides should be considered where possible:
1) The acquisition of a Hazardous Materials Storage (HMS) Building
2) The construction of a new Pesticide Storage Facility.
(1) Hazardous Material Storage (HMS) Building
Free standing hazardous materials storage buildings composed of heavy duty steel frames with twelve gauge steel roof and walls are available commercially. The building should ideally have a two hour fire rating. Secondary containment is achieved by means of sumps or grated floors. Doors are self closing and can be locked.
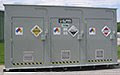
Prefabricated chemical storage building
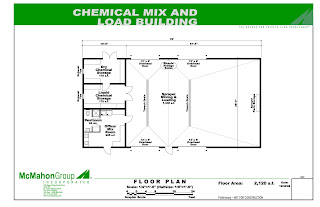
Typical Chemical Mix and Load Building
It is important to consult with an engineer or licensed contractor familiar with the state and local building code requirements before implementing any plan. Before construction begins, consult with local agencies that deal with planning, zoning, wetlands, health and fire regulations. Buildings used for the storage of pesticides should be fire rated in accordance with NFPA 30 ASTM E119 - 08a and International Building Code Type H-1. A properly designed storage area should be built with regard for worker safety and protection of the environment and public health. It should, at a minimum, facilitate the secure, dry storage of pesticides and safe conditions for workers with easy access to worker Personal Protective Equipment (PPE), secondary containment of incidental spills due to normal mixing / loading practices and secondary containment of large accidental spills.
Containment
The building should provide adequate within-building spill containment. In the event of an accident or major spillage, the building should be capable of containing 125% of the volume of the largest container. This can be achieved by surrounding the storage room floor with a 4 to 8 inch curb and / or by a grated trench which drains to a sump. If possible the floor should slope slightly to the center. A change in floor perimeter to sump slope of 0.5% is advisable. These measures will also prevent water or other liquids from seeping or flowing onto the storage area. The storage facility should be constructed in such a way that run-off from fire streams will not contaminate streams, ponds, groundwater, croplands or buildings.
Walls
The storage building should be separated as much as is reasonably possible from other use areas. The building should be designed to prevent against potential fires due to storage of flammable pesticides within the building and from fire in adjacent buildings. A fire wall slows the spread of fire from one area to another. It is recommended that a storage building with a 1-hour fire wall should be located at least fifty feet from other buildings. For a 2-hour fire wall, the set back distance should be twenty five feet.
4 Hour Fire Wall
For a 4 hour fire wall (highly recommended), there is no minimum setback distance. The building should be accessible from all sides for emergency and fire fighting equipment.
Hollow Masonry Definition: Less than 75% solid cross section or greater than 25% void.
Solid Masonry Definition: Greater than 75% solid cross section or less than 25% void.
Gypsum wallboards of 5/8" thickness on both sides of the wall constitute a one hour rated firewall. Two gypsum wallboards on both sides are considered to be 2 hour rated fire wall. An untreated or unlined gypsum wallboard or wood product wall type is not recommended for any wall surface except to partition indoor office or non chemical dry storage area. The interior wall surfaces should be impervious to pesticides and easily cleaned. Suitable wall liners applied over gypsum wallboard are painted steel, aluminum, fiberglass, or high density plastic panels.
Doors
The interior doors should be windowless, steel (solid core), at least 36" wide, set in a steel frame and open to the outside. Exterior doors should be windowless; steel (solid core) one door set to temporary storage should be an overhead or double door to allow access of palletized chemical products. Exterior passage doors should be fitted with self-closing and locking mechanisms. A manual device to hold doors open during pesticide movement from place-to-place is recommended.
Overhead doors should be steel roll up type as opposed to commercial section steel or fiberglass construction. Powered door lifts can extend the life of overhead doors and offer a greater degree of operator safety and security.
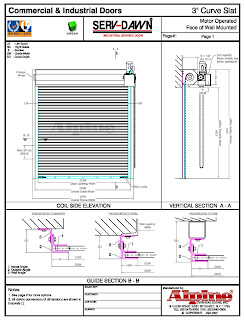
Steel Roll-Up Door
Floors & Concrete Specifications
The storage building floors should be water tight, chemically impervious and skid resistant. Concrete floors with an impervious sealant or some other material of comparable strength and impermeability should be used. The following specifications should be used for concrete:
• Type I or Type II high quality cement with 5 - 7.5% air entrainment (this improves water tightness) and compressive strength of 4,000 - 4,500 psi
• Water - cement ratio of 0.40-0.45 for a stiff (1.5" - 3") slump; a relatively dry mix for maximum strength, pesticide and fertilizer resistance, freeze / thaw resistance and water tightness
While concrete is durable, it will deteriorate over time. Liquid fertilizers are the main cause of concrete deterioration. However, pesticides can contaminate concrete and leak through cracks into groundwater. Protective coatings for concrete seal the surface and help prevent the corrosive actions of pesticides and fertilizers on concrete. Among the coatings commercially available are epoxies, urethanes, polyesters, vinyls, chlorosulfonated polyethylene, and polyureas. The appropriate type of coating will depend on the types of pesticides and fertilizers being stored and should be determined in consultation with a distributor.
At the entrance to the overhead doors should be a ramped section of concrete that extends into the building approximately 6 inches pitched towards the door. This 6 inch ramp will shed water away from the mix and storage area from melting snow and rain. Water entering the building would be considered rinsate and must be treated for reuse.
Flexible water stops should be installed at all control joints and in floor to wall joints. A perimeter concrete curb in storage areas should be a minimum of 8 inches in height to contain any accidental release of concentrated chemicals or finished spray preparations in storage.
Lighting
Lighting should be bright enough so that labels may be easily read. The lighting and exhaust system should be turned on by the same switch located on the outside of the entry door to the chemical storage area. The switch should be equipped with a signal light indicating the exhaust system is on and functioning properly.
Electrical Design
Electrical equipment and wiring should be designed to explosion proof. The wires should be shielded in approved electrical conduit. An exterior electrical service disconnect in a locked National Electric Manufacturers Association (NEMA) rated, weather proof box should be provided.
The pad should be curbed to a sufficient height in order to contain spills, leaks, releases or other discharges that are generated during the mixing and loading of pesticides and to prevent water or other liquids from flowing onto and off of the surface.
To avoid rainwater mixing with pesticides, it is recommended that the area be roofed. Roof overhangs should be at least a thirty degree angle from vertical from the edge of the mixing/loading pad in all directions Containment needs may be further met by constructing the pad in such a way that it slopes (at least 2%) to a single liquid tight sump.
Example of dimensions of a mix / load pad with a length of 30 feet a width of 20 feet with a pad slope of 3% to a center sump, a curb of 3 inches high and 24 inches wide will contain a total of 717 gallons.
Sump Designs
The pad should slope to a water tight sump or catch basin. The purpose of a sump is to collect the spilled material and facilitate its reuse. Collected rinsates should be pumped to an above ground holding tank and reused for mixing subsequent loads or field applied at lowest reasonable rates. The sump pump should be capable of transferring the liquid to the holding tank from the sump at a rate equivalent to the fastest sump filling rate. The tanks should not be filled beyond 95% of their capacity to allow for thermal expansion and must be placed on a concrete or other impervious surfaced floor on stands or on a raised platform to allow the detection of leaks from, or water in or under, the pesticide container.
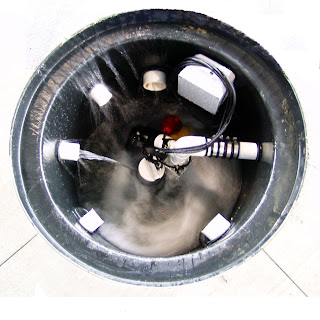
Example of Below Grade Sump System
A single sump can be placed monolithically with the mixing/loading pad or a precast concrete or prefabricated steel sump could be installed before the concrete pad is placed. Precast concrete sumps are built in a range of sizes with capacities up to 100 gallons. A double lined stainless steel sump allows the monitoring by inspection of potential leaks from the sump. Most have a capacity of thirty gallons.
The sump should be kept clean to avoid the creation of sludge due to dirt, mud, trash, rocks or grass clippings. Sludge is considered to be a hazardous waste if contaminated by unknown or incompatible pesticides. If the sludge is contaminated by only one pesticide or a compatible mix, the material can be applied to the land at or below the label rate. To reduce sludge problems in sumps where application vehicles are washed, some facilities may elect to install two sumps in series. Sumps should be kept clean as contaminated soil and debris in sumps creates a serious hazardous waste disposal problem. In addition, the sump should be covered with a structural grate to ensure safety. The grate could be covered with a finer mesh dust cover. The sump should be kept covered and cleaned out especially during spraying season.
Washing and Rinsing Operations
Washing and rinsing of pesticide residues from application equipment, mixing equipment or other items used in storing, handling or transporting pesticides should occur on the pad.
Protection of Water Supplies
No pesticide application equipment or mix tank should be filled directly from any source waters unless a double back siphon prevention device is present. Additionally, an air gap between full tank level and water source device is recommended.
Non-Liquid Pesticides
If non-liquid pesticides (fertilizer combination pesticides, dry granular application types) are loaded the spill containment surface may consist of a tarpaulin made of non-absorbent materials which is of adequate thickness to withstand all foreseeable loading conditions.
Pesticide Handling Instructions
Materials Safety Data Sheets (MSDS) for each pesticide should be on file and posted in a prominent location. At a minimum the employer should have posted the product label and physical and health hazards associated with the pesticides being used. The measures employees can take to protect themselves from these hazards, including safety precautions and protective work procedures, should be posted.
Emergency Response Plan
An emergency response plan should be developed. Such a plan lists actions to take and personnel to contact in the event of a spill or accident. The plan should begin with a current listing of the pesticides used or stored at the facility and should include the following information:
• Names and quantities of pesticides;
• Location of the property including a map with directions;
• Names, addresses and telephone numbers of the owner and key employees;
• Plan of the facility showing pesticides locations, flammable materials, electrical service, water supply, fuel storage tanks, fire hydrants, storm drains, and nearby wetlands, ponds, or streams;
• Location of emergency equipment supplies including breathing equipment and protective equipment;
Copies of the emergency response plan should be located near the entrance to the pesticide facility and with business records. Copies should also be given to the local police department and fire department. Contacts should include the following: fire department; police; spill clean up firm; nearest hospital; pesticide bureau; board of health; owner and or manager of the facility;
The plan should be available in both English and the language or languages understood by workers if this is not English.
Fire Prevention
An automatic smoke detection system or smoke and heat detection system should be installed. The appropriate fire prevention and emergency procedures should be developed in consultation with the local fire department. Suitable methods for extinguishing fires should be installed, such as the appropriate type and number of fire extinguishers. The number and placement of fire extinguishers should conform to the National Fire Protection Association Standard No. 10. All electrical fixtures and appliances should be explosion-proof units approved for use in facilities storing flammable and combustible liquids.
In the event of a fire it is frequently more environmentally sound to allow the fire to burn itself out if it can be contained within the area. This avoids the likelihood of pesticides being released into the ground as a result of water being added. Dry chemical fire suppression systems are superior in chemical storage areas.
Personal Safety
Personal protection equipment such as respirators, chemical resistant (CR) gloves, CR footwear, coveralls with long sleeves, protective eyewear, CR headgear, CR aprons and a first-aid kit should be available immediately outside the storage area. The first-aid kit should include the following items: adhesive strips, tape, ammonia inhalant, eye pads, burn cream, gauze bandages and tweezers. Gloves should be made of rubber, neoprene or other chemical resistant material. It is essential that protective eyewear be worn during mixing/loading. The protective eyewear should consist of safety glasses that provide front, brow and temple protection, goggles or a face shield.
Workers should be instructed in the correct procedure for the removal of contaminated clothing. Eye wash stations or portable eye wash bottles should be easily accessed by each person engaged in the operation and should be capable of flushing eyes for a minimum of fifteen minutes. Drench showers should be located at or near storage and mixing location. Routine wash up facilities, equipped with soap, hand cleanser and single use paper towels should be available near the storage area.
Record Keeping
A daily record of all chemical applications should be located on premises, preferably away from chemical storage areas. All chemical discharges to the environment or spills should be recorded. The records should include chemical or chemicals, the date and time of the incident and the cleanup method.
Accident Response
An absorbent material such as re-usable gelling agents, vermiculite, clay, pet litter, activated charcoal or commercially available spill containment kit should be on hand along with an approved recovery drum and shovel to quickly contain and clean up any small spills.
Security
The chemical storage area should be kept locked when not currently being used by a qualified applicator and the door to the storage area should contain a weather proof sign warning of the existence and danger of pesticides inside. The sign should be visible at a distance of twenty five feet and should read as follows:
DANGER
PESTICIDE STORAGE
AREA and MIXING AREA
ALL UNAUTHORIZED
PERSONS KEEP OUT
KEEP DOORS LOCKED
WHEN NOT IN USE
The sign should be posted in both English and the language or languages understood by workers if this is not English.
While the above has illustrated basic guidelines for the safe storage and mixing of golf turf chemicals they are not intended to be complete or definitive in identifying all hazards associated with your club, preventing workplace accidents, or complying with any safety related, or other, laws or regulations. You are encouraged to alter them to fit the specific hazards or situations of your club and to have your legal counsel review all of your plans and club policies.
Literature sited in the composition of this article:

No other area on the golf course property is as liability sensitive and environmentally worthy of proper planning and scrutiny as the area where golf course chemicals and fertilizers are stored, mixed and loaded for application to the turf. Knowledgeable and expert design in relation to size, space and components will safeguard workers, members and the environment against the event of an unintended chemical release.
Inadequately stored pesticides and improper chemical mixing and loading practices can present a potential risk to co-worker health and to environment. The quality of surface water, groundwater, soil and air can be damaged in areas where pesticides are stored under inappropriate conditions, improperly mixed and loaded into application tanks and where equipment are washed and rinsed after application. Uncontrolled releases or leakages may have serious health and environmental consequences.
The purpose of this document is to provide guidance to golf course superintendents looking for information on appropriate techniques and approaches for the mixing, loading and storage of pesticides. These guidelines were prepared with input from written resources, individuals and organizations with a broad range of expertise and experience. It is a compilation of the best information available regarding the mixing, loading and storage of pesticides. The result is a set of guidelines which represents a general consensus on how pesticide mixing, loading and storage issues should be approached. It is important to remember that mixing, loading and storage needs will vary greatly from golf course to golf course and site to site. No document could specify exactly what approach should be taken in each situation. As such, it should be kept in mind that this document is intended as general guideline only. These are recommendations, not standards or regulations and as such can and should be adjusted to meet individual golf course needs. These recommendations are designed to assist golf course superintendents in managing, renovating and building their storage areas and conduct their mixing and loading operations in ways that will help minimize exposure to pesticides and reduce the risks to public health and the environment. These are not intended to be regulations of any federal, state or local regulatory agency.
The safest approach to any pesticide storage plan is to limit the amounts and types of pesticides stored. The amounts and types of pesticides stored should be maintained at the level that is immediately required and should not be stored beyond short-term needs.
Selecting a Storage Location
An existing or proposed area should be carefully evaluated to determine its suitability for pesticide handling and storage. In particular the potential harm to human health and the environment due to spills, contaminated runoff or fires should be assessed. If possible, the area should be located at least four hundred feet from any public or private drinking water supplies and two hundred from surface water. Separation from water resources should be greater in areas of sandy, rocky or light textured, rapidly draining soils. Whenever feasible, the area should not be located in a 100 year floodplain. Runoff from adjacent areas resulting from a 25 year 24 hour storm (2.9 - 3.6 inches of rainfall) should be diverted around the facility. The site location should be accessible in the event of a fire or any another emergency situation. The pesticide storage area should be protected against direct sunlight, freezing temperatures and extreme heat. Temperatures in the storage area should be kept between 40F and 100F. Pesticides should not be stored outdoors. Where practical, the mixing/loading area should be located in close proximity to or physically attached to the chemical storage facility to minimize the distance that chemicals are transported to combine finished spray mixes. Consideration should also be given to the additional area required by a mixing/loading pad when selecting the site for pesticide storage.
Storage Practices
Pesticide storage should be restricted to a first story room or area which has direct access to the outside. Pesticides should never be stored in basements. Pesticides should be stored in accordance with their label requirements in their original container with the original label attached and clearly visible. They should always be kept off the ground to prevent the accumulation of water in or under the containers. Separation of pesticides by hazard and function is essential. Flammable pesticides should be stored separately from non-flammable pesticides, preferable in a fire proof cabinet. Dry pesticides should be stored above and separately from liquid pesticides to avoid wetting from spills. Fungicides, herbicides and insecticides should be stored in separate locations of the storage area to prevent cross contamination and accidental misuse. Pesticides should be stored away from fertilizer, potable water supplies, seeds and personal protective equipment (PPE) to avoid cross-contamination. Particular care should be taken when storing petroleum based emulsifiable concentrate chemicals due to their potential high volatility. Pesticides should not be stored in the same place as ammonium nitrate fertilizer. Exposure to sunlight can cause pesticides to chemically breakdown. Windows are not recommended in pesticide storage areas do to light infiltration / chemical degradation and security reasons. Because shelf life is difficult to predict, pesticides should not be stored longer than two years.
Two options for storing pesticides should be considered where possible:
1) The acquisition of a Hazardous Materials Storage (HMS) Building
2) The construction of a new Pesticide Storage Facility.
(1) Hazardous Material Storage (HMS) Building
Free standing hazardous materials storage buildings composed of heavy duty steel frames with twelve gauge steel roof and walls are available commercially. The building should ideally have a two hour fire rating. Secondary containment is achieved by means of sumps or grated floors. Doors are self closing and can be locked.
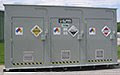
Prefabricated chemical storage building
The walls have air vents or ventilation fans for improved circulation and relief of gaseous vapor build up. Generally the capacities of the HMS buildings vary from under 30 ft² to over 600 ft². Options on these buildings are varied and can be added as required.
(2) Construction of a New Pesticide Storage Facility (general recommendations)
(2) Construction of a New Pesticide Storage Facility (general recommendations)
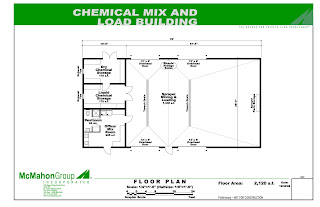
Typical Chemical Mix and Load Building
It is important to consult with an engineer or licensed contractor familiar with the state and local building code requirements before implementing any plan. Before construction begins, consult with local agencies that deal with planning, zoning, wetlands, health and fire regulations. Buildings used for the storage of pesticides should be fire rated in accordance with NFPA 30 ASTM E119 - 08a and International Building Code Type H-1. A properly designed storage area should be built with regard for worker safety and protection of the environment and public health. It should, at a minimum, facilitate the secure, dry storage of pesticides and safe conditions for workers with easy access to worker Personal Protective Equipment (PPE), secondary containment of incidental spills due to normal mixing / loading practices and secondary containment of large accidental spills.
Containment
The building should provide adequate within-building spill containment. In the event of an accident or major spillage, the building should be capable of containing 125% of the volume of the largest container. This can be achieved by surrounding the storage room floor with a 4 to 8 inch curb and / or by a grated trench which drains to a sump. If possible the floor should slope slightly to the center. A change in floor perimeter to sump slope of 0.5% is advisable. These measures will also prevent water or other liquids from seeping or flowing onto the storage area. The storage facility should be constructed in such a way that run-off from fire streams will not contaminate streams, ponds, groundwater, croplands or buildings.
Walls
The storage building should be separated as much as is reasonably possible from other use areas. The building should be designed to prevent against potential fires due to storage of flammable pesticides within the building and from fire in adjacent buildings. A fire wall slows the spread of fire from one area to another. It is recommended that a storage building with a 1-hour fire wall should be located at least fifty feet from other buildings. For a 2-hour fire wall, the set back distance should be twenty five feet.
4 Hour Fire Wall
For a 4 hour fire wall (highly recommended), there is no minimum setback distance. The building should be accessible from all sides for emergency and fire fighting equipment.
Hollow Masonry Definition: Less than 75% solid cross section or greater than 25% void.
Solid Masonry Definition: Greater than 75% solid cross section or less than 25% void.
Gypsum wallboards of 5/8" thickness on both sides of the wall constitute a one hour rated firewall. Two gypsum wallboards on both sides are considered to be 2 hour rated fire wall. An untreated or unlined gypsum wallboard or wood product wall type is not recommended for any wall surface except to partition indoor office or non chemical dry storage area. The interior wall surfaces should be impervious to pesticides and easily cleaned. Suitable wall liners applied over gypsum wallboard are painted steel, aluminum, fiberglass, or high density plastic panels.
Doors
The interior doors should be windowless, steel (solid core), at least 36" wide, set in a steel frame and open to the outside. Exterior doors should be windowless; steel (solid core) one door set to temporary storage should be an overhead or double door to allow access of palletized chemical products. Exterior passage doors should be fitted with self-closing and locking mechanisms. A manual device to hold doors open during pesticide movement from place-to-place is recommended.
Overhead doors should be steel roll up type as opposed to commercial section steel or fiberglass construction. Powered door lifts can extend the life of overhead doors and offer a greater degree of operator safety and security.
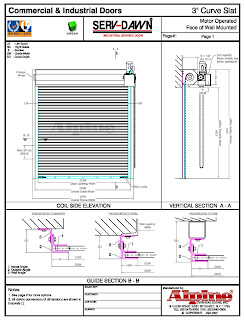
Steel Roll-Up Door
Floors & Concrete Specifications
The storage building floors should be water tight, chemically impervious and skid resistant. Concrete floors with an impervious sealant or some other material of comparable strength and impermeability should be used. The following specifications should be used for concrete:
• Type I or Type II high quality cement with 5 - 7.5% air entrainment (this improves water tightness) and compressive strength of 4,000 - 4,500 psi
• Water - cement ratio of 0.40-0.45 for a stiff (1.5" - 3") slump; a relatively dry mix for maximum strength, pesticide and fertilizer resistance, freeze / thaw resistance and water tightness
While concrete is durable, it will deteriorate over time. Liquid fertilizers are the main cause of concrete deterioration. However, pesticides can contaminate concrete and leak through cracks into groundwater. Protective coatings for concrete seal the surface and help prevent the corrosive actions of pesticides and fertilizers on concrete. Among the coatings commercially available are epoxies, urethanes, polyesters, vinyls, chlorosulfonated polyethylene, and polyureas. The appropriate type of coating will depend on the types of pesticides and fertilizers being stored and should be determined in consultation with a distributor.
At the entrance to the overhead doors should be a ramped section of concrete that extends into the building approximately 6 inches pitched towards the door. This 6 inch ramp will shed water away from the mix and storage area from melting snow and rain. Water entering the building would be considered rinsate and must be treated for reuse.
Flexible water stops should be installed at all control joints and in floor to wall joints. A perimeter concrete curb in storage areas should be a minimum of 8 inches in height to contain any accidental release of concentrated chemicals or finished spray preparations in storage.
Lighting
Lighting should be bright enough so that labels may be easily read. The lighting and exhaust system should be turned on by the same switch located on the outside of the entry door to the chemical storage area. The switch should be equipped with a signal light indicating the exhaust system is on and functioning properly.
Electrical Design
Electrical equipment and wiring should be designed to explosion proof. The wires should be shielded in approved electrical conduit. An exterior electrical service disconnect in a locked National Electric Manufacturers Association (NEMA) rated, weather proof box should be provided.
Security and Fire Control
A system should be installed to monitor doors and interior spaces for unintended intruders. Door sensors and motion detection is the preferred systems. These intrusion warning systems can be installed to contact management or police in the event of unauthorized intrusion.
A fire control and alarm system is also recommended. By nature of chemical composition of stored liquid and dry pesticides a dry fire suppression system is recommended. A direct call system to local fire protection district is advisable.
Temperature
Area temperatures should be kept below 100 F and above pesticide freezing points. An electrical heater can be used to keep the temperature above 40 F during the winter. Open flame heaters should never be used. Air conditioning may be needed during the summer to prevent the volatilization of pesticides, if this is likely to be a problem.
Ventilation Design
For safety and protection, good air ventilation should be present at the facility. The area should have an operating ventilation system sufficient to prevent the accumulation of vapors and to control temperature. Ventilation should be provided by means of fans. The fans should operate off the same switch as the lighting system. An air inlet should be located within 12" of the floor to facilitate the escape of heavier than air vapors. During occupancy, the ventilation system should provide a minimum of 6 air changes per hour.
Bulk Containers
Storage and rinsate containers and appurtenances such as valves, fittings, pipes and hoses, should be installed and maintained so as to prevent the discharge of liquid pesticides, finished spray mixes and rinsate. As such they should be structurally sound, resistant to changes in temperature extremes and be constructed of materials that are resistant to corrosion, puncture or cracking. Stainless steel, fiberglass, polyethylene, and lined ferrous metal are acceptable. Valves on storage containers should be locked or otherwise secured except during times of authorized access.
Mixing and Loading Facilities
Contamination of soil, groundwater and surface water can result from small quantities of pesticides spilled regularly in areas where pesticides are mixed and loaded into applicator tanks and where equipment is washed and rinsed after application. Spills or overflows can lead to the accumulation of pesticides in the soil and possible drinking water supplies.
Mixing / Loading Location
Mixing and loading should be avoided in areas where a spill, a leak or overflow could allow pesticides to get into water systems. The mixing and loading of pesticides should not occur within four hundred feet of any private or public drinking water supply or two hundred feet of surface water. No pesticide application equipment or mix tank should be filled directly from any source waters unless a back siphon prevention device is present. Mixing and loading should not occur on gravel driveways or on other surfaces that allow spills to move quickly through the soil. Prior to building a mixing and loading facility it is advisable to install and maintain test wells near the site to have the ability to monitor ground water quality. A sample boring of soil to test for chemical contaminants is also recommended before construction.
Mixing / Loading Practices
Mixing or loading of pesticides should be avoided in areas where a spill, leak or overflow could allow pesticides to get into water systems. All transfers of pesticides between containers, including mixing, loading and equipment cleaning, should be conducted over a spill containment surface designed to intercept, retain and recover spillage, leakage and wash water.
Appropriate personal protective equipment (PPE) should be worn before opening a pesticide container, check product label for appropriate PPE. The label should be checked for Use Restrictions. PPE may include front protection such as a bib top apron made of butyl, nitrile, or foil laminate material. A face shield, shielded safety glasses or goggles should be worn. When pouring any pesticide from its container, container and pesticide should be kept below face level. A respirator will ensure protection against dusts or vapors per label requirements. The container should be closed or sealed after each use. A tank should never be left unattended while it is being filled. If the pesticide user should splash or spill pesticides on his person, he should stop the operation, wash thoroughly with a mild liquid detergent and water or as advised on the product label, put on clean PPE and clean up the spill. Containment needs depend on the quantities of pesticides that are being mixed and loaded. If mixing small quantities, a tarpaulin can be sufficient to contain any spills. Spills can be then cleaned up with an absorbent material or commercially available chemical release control kit. If mixing large quantities regularly, the construction of a mixing/loading pad is an option to consider.
Construction of a Mixing/ Loading Pad
It is important to consult with an engineer or licensed contractor familiar with the state building code requirements before implementing any plan. Before construction begins, consult with local agencies that deal with planning, zoning, wetlands, health and fire. If pesticides are often mixed and loaded in the same place, or application equipment is cleaned in the one spot, a permanent pesticide mixing / loading pad is a sound option. Spill clean ups can be made easier, and pesticide waste can be reduced and reused. They can also prevent the harm that spills and runoff can cause to the environment or to people. The area should be located at least four hundred feet (preferably down hill) from any public or private drinking water supplies and two hundred feet (preferably down hill) from surface water. It should not be located within any residential area or other sensitive area (such as feedlots, animal shelters, play areas, schools). For obvious reasons areas prone to flooding should be avoided for construction of permanent mixing / loading pad.
Design
The design of the pad should be a function of the operations performed at the site – the number and volume of different pesticides stored and applied the rinsing procedures, the size of the spray boom- and also the weather conditions, especially the levels of precipitation and freezing conditions. The pad should be located adjacent to the storage area. It is recommended that the pad be constructed of an impervious material such as sealed concrete. The pad should remain intact under freezing conditions. The following concrete specifications should be followed to ensure a water tight pad and good surface durability:
• Type I or Type II high quality cement with 5 - 7.5% air entrainment (this improves water tightness) and compressive strength of 4,000 -
4,500 psi;
• Water- cement ratio of 0.40-0.45 for a stiff (1.5" - 3") slump; a relatively dry mix for maximum strength, pesticide and fertilizer resistance, freeze/thaw resistance and water tightness;
• The subgrade (original ground) upon which the pad will be placed must be dense, uniform and relatively free draining to provide a good foundation for the concrete pad. If the subgrade is not adequate a sub-base material should be installed consisting of 4 inches of well compacted clean sand, gravel or sand and gravel mixture;
• The subgrade or sub-base should be moistened immediately prior to concrete placement to minimize shrinkage and cracking potential;
• Large coarse aggregate (1 to 1.5 inches) which permits a lower water content and reduces the potential for cracking should be used;
• Reinforcing steel should be placed two inches from the top of the pad. Reinforcing bars (supported #4 bars at 15 to 18 inch spacing) are superior to wire mesh for proper location of the steel in the slab and to allow workers to step between the bars. Reinforcing steel will keep shrinkage cracks closed if properly located;
• A high level of workmanship should be ensured during concrete placement and curing of the pad.
While concrete is durable, it will deteriorate over time. Pesticides can contaminate concrete and leak through cracks into groundwater. Protective coatings for concrete seal the surface and help prevent the corrosive actions of pesticides and fertilizers on concrete. Among the coatings commercially available are epoxies, urethanes, polyesters, vinyls, chlorosulfonated polyethylene, and polyureas. The appropriate type of coating will depend on the types of pesticides being used and should be determined in consultation with a distributor.
Containment Volume
The total mixing / loading area containment volume should be 1.25 times the volume of the largest tank to be loaded in the area. If the area is not protected from contact with precipitation, the containment volume should be equal to the volume generated by a 2 year 24 hour storm (2.9 - 3.6 inches of rainfall). If the rainwater mixes with a single known pesticide or compatible pesticides (i.e., pesticides with at least one common use site on their labels) the mixture can be applied to the field at or below the label rate.
A system should be installed to monitor doors and interior spaces for unintended intruders. Door sensors and motion detection is the preferred systems. These intrusion warning systems can be installed to contact management or police in the event of unauthorized intrusion.
A fire control and alarm system is also recommended. By nature of chemical composition of stored liquid and dry pesticides a dry fire suppression system is recommended. A direct call system to local fire protection district is advisable.
Temperature
Area temperatures should be kept below 100 F and above pesticide freezing points. An electrical heater can be used to keep the temperature above 40 F during the winter. Open flame heaters should never be used. Air conditioning may be needed during the summer to prevent the volatilization of pesticides, if this is likely to be a problem.
Ventilation Design
For safety and protection, good air ventilation should be present at the facility. The area should have an operating ventilation system sufficient to prevent the accumulation of vapors and to control temperature. Ventilation should be provided by means of fans. The fans should operate off the same switch as the lighting system. An air inlet should be located within 12" of the floor to facilitate the escape of heavier than air vapors. During occupancy, the ventilation system should provide a minimum of 6 air changes per hour.
Bulk Containers
Storage and rinsate containers and appurtenances such as valves, fittings, pipes and hoses, should be installed and maintained so as to prevent the discharge of liquid pesticides, finished spray mixes and rinsate. As such they should be structurally sound, resistant to changes in temperature extremes and be constructed of materials that are resistant to corrosion, puncture or cracking. Stainless steel, fiberglass, polyethylene, and lined ferrous metal are acceptable. Valves on storage containers should be locked or otherwise secured except during times of authorized access.
Mixing and Loading Facilities
Contamination of soil, groundwater and surface water can result from small quantities of pesticides spilled regularly in areas where pesticides are mixed and loaded into applicator tanks and where equipment is washed and rinsed after application. Spills or overflows can lead to the accumulation of pesticides in the soil and possible drinking water supplies.
Mixing / Loading Location
Mixing and loading should be avoided in areas where a spill, a leak or overflow could allow pesticides to get into water systems. The mixing and loading of pesticides should not occur within four hundred feet of any private or public drinking water supply or two hundred feet of surface water. No pesticide application equipment or mix tank should be filled directly from any source waters unless a back siphon prevention device is present. Mixing and loading should not occur on gravel driveways or on other surfaces that allow spills to move quickly through the soil. Prior to building a mixing and loading facility it is advisable to install and maintain test wells near the site to have the ability to monitor ground water quality. A sample boring of soil to test for chemical contaminants is also recommended before construction.
Mixing / Loading Practices
Mixing or loading of pesticides should be avoided in areas where a spill, leak or overflow could allow pesticides to get into water systems. All transfers of pesticides between containers, including mixing, loading and equipment cleaning, should be conducted over a spill containment surface designed to intercept, retain and recover spillage, leakage and wash water.
Appropriate personal protective equipment (PPE) should be worn before opening a pesticide container, check product label for appropriate PPE. The label should be checked for Use Restrictions. PPE may include front protection such as a bib top apron made of butyl, nitrile, or foil laminate material. A face shield, shielded safety glasses or goggles should be worn. When pouring any pesticide from its container, container and pesticide should be kept below face level. A respirator will ensure protection against dusts or vapors per label requirements. The container should be closed or sealed after each use. A tank should never be left unattended while it is being filled. If the pesticide user should splash or spill pesticides on his person, he should stop the operation, wash thoroughly with a mild liquid detergent and water or as advised on the product label, put on clean PPE and clean up the spill. Containment needs depend on the quantities of pesticides that are being mixed and loaded. If mixing small quantities, a tarpaulin can be sufficient to contain any spills. Spills can be then cleaned up with an absorbent material or commercially available chemical release control kit. If mixing large quantities regularly, the construction of a mixing/loading pad is an option to consider.
Construction of a Mixing/ Loading Pad
It is important to consult with an engineer or licensed contractor familiar with the state building code requirements before implementing any plan. Before construction begins, consult with local agencies that deal with planning, zoning, wetlands, health and fire. If pesticides are often mixed and loaded in the same place, or application equipment is cleaned in the one spot, a permanent pesticide mixing / loading pad is a sound option. Spill clean ups can be made easier, and pesticide waste can be reduced and reused. They can also prevent the harm that spills and runoff can cause to the environment or to people. The area should be located at least four hundred feet (preferably down hill) from any public or private drinking water supplies and two hundred feet (preferably down hill) from surface water. It should not be located within any residential area or other sensitive area (such as feedlots, animal shelters, play areas, schools). For obvious reasons areas prone to flooding should be avoided for construction of permanent mixing / loading pad.
Design
The design of the pad should be a function of the operations performed at the site – the number and volume of different pesticides stored and applied the rinsing procedures, the size of the spray boom- and also the weather conditions, especially the levels of precipitation and freezing conditions. The pad should be located adjacent to the storage area. It is recommended that the pad be constructed of an impervious material such as sealed concrete. The pad should remain intact under freezing conditions. The following concrete specifications should be followed to ensure a water tight pad and good surface durability:
• Type I or Type II high quality cement with 5 - 7.5% air entrainment (this improves water tightness) and compressive strength of 4,000 -
4,500 psi;
• Water- cement ratio of 0.40-0.45 for a stiff (1.5" - 3") slump; a relatively dry mix for maximum strength, pesticide and fertilizer resistance, freeze/thaw resistance and water tightness;
• The subgrade (original ground) upon which the pad will be placed must be dense, uniform and relatively free draining to provide a good foundation for the concrete pad. If the subgrade is not adequate a sub-base material should be installed consisting of 4 inches of well compacted clean sand, gravel or sand and gravel mixture;
• The subgrade or sub-base should be moistened immediately prior to concrete placement to minimize shrinkage and cracking potential;
• Large coarse aggregate (1 to 1.5 inches) which permits a lower water content and reduces the potential for cracking should be used;
• Reinforcing steel should be placed two inches from the top of the pad. Reinforcing bars (supported #4 bars at 15 to 18 inch spacing) are superior to wire mesh for proper location of the steel in the slab and to allow workers to step between the bars. Reinforcing steel will keep shrinkage cracks closed if properly located;
• A high level of workmanship should be ensured during concrete placement and curing of the pad.
While concrete is durable, it will deteriorate over time. Pesticides can contaminate concrete and leak through cracks into groundwater. Protective coatings for concrete seal the surface and help prevent the corrosive actions of pesticides and fertilizers on concrete. Among the coatings commercially available are epoxies, urethanes, polyesters, vinyls, chlorosulfonated polyethylene, and polyureas. The appropriate type of coating will depend on the types of pesticides being used and should be determined in consultation with a distributor.
Containment Volume
The total mixing / loading area containment volume should be 1.25 times the volume of the largest tank to be loaded in the area. If the area is not protected from contact with precipitation, the containment volume should be equal to the volume generated by a 2 year 24 hour storm (2.9 - 3.6 inches of rainfall). If the rainwater mixes with a single known pesticide or compatible pesticides (i.e., pesticides with at least one common use site on their labels) the mixture can be applied to the field at or below the label rate.
The pad should be curbed to a sufficient height in order to contain spills, leaks, releases or other discharges that are generated during the mixing and loading of pesticides and to prevent water or other liquids from flowing onto and off of the surface.
To avoid rainwater mixing with pesticides, it is recommended that the area be roofed. Roof overhangs should be at least a thirty degree angle from vertical from the edge of the mixing/loading pad in all directions Containment needs may be further met by constructing the pad in such a way that it slopes (at least 2%) to a single liquid tight sump.
Example of dimensions of a mix / load pad with a length of 30 feet a width of 20 feet with a pad slope of 3% to a center sump, a curb of 3 inches high and 24 inches wide will contain a total of 717 gallons.
Sump Designs
The pad should slope to a water tight sump or catch basin. The purpose of a sump is to collect the spilled material and facilitate its reuse. Collected rinsates should be pumped to an above ground holding tank and reused for mixing subsequent loads or field applied at lowest reasonable rates. The sump pump should be capable of transferring the liquid to the holding tank from the sump at a rate equivalent to the fastest sump filling rate. The tanks should not be filled beyond 95% of their capacity to allow for thermal expansion and must be placed on a concrete or other impervious surfaced floor on stands or on a raised platform to allow the detection of leaks from, or water in or under, the pesticide container.
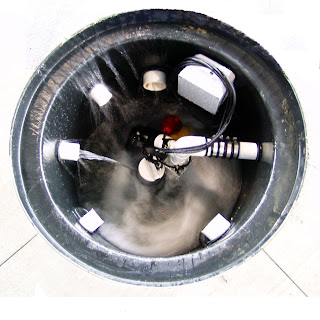
Example of Below Grade Sump System
A single sump can be placed monolithically with the mixing/loading pad or a precast concrete or prefabricated steel sump could be installed before the concrete pad is placed. Precast concrete sumps are built in a range of sizes with capacities up to 100 gallons. A double lined stainless steel sump allows the monitoring by inspection of potential leaks from the sump. Most have a capacity of thirty gallons.
The sump should be kept clean to avoid the creation of sludge due to dirt, mud, trash, rocks or grass clippings. Sludge is considered to be a hazardous waste if contaminated by unknown or incompatible pesticides. If the sludge is contaminated by only one pesticide or a compatible mix, the material can be applied to the land at or below the label rate. To reduce sludge problems in sumps where application vehicles are washed, some facilities may elect to install two sumps in series. Sumps should be kept clean as contaminated soil and debris in sumps creates a serious hazardous waste disposal problem. In addition, the sump should be covered with a structural grate to ensure safety. The grate could be covered with a finer mesh dust cover. The sump should be kept covered and cleaned out especially during spraying season.
Washing and Rinsing Operations
Washing and rinsing of pesticide residues from application equipment, mixing equipment or other items used in storing, handling or transporting pesticides should occur on the pad.
Protection of Water Supplies
No pesticide application equipment or mix tank should be filled directly from any source waters unless a double back siphon prevention device is present. Additionally, an air gap between full tank level and water source device is recommended.
Non-Liquid Pesticides
If non-liquid pesticides (fertilizer combination pesticides, dry granular application types) are loaded the spill containment surface may consist of a tarpaulin made of non-absorbent materials which is of adequate thickness to withstand all foreseeable loading conditions.
Pesticide Handling Instructions
Materials Safety Data Sheets (MSDS) for each pesticide should be on file and posted in a prominent location. At a minimum the employer should have posted the product label and physical and health hazards associated with the pesticides being used. The measures employees can take to protect themselves from these hazards, including safety precautions and protective work procedures, should be posted.
Emergency Response Plan
An emergency response plan should be developed. Such a plan lists actions to take and personnel to contact in the event of a spill or accident. The plan should begin with a current listing of the pesticides used or stored at the facility and should include the following information:
• Names and quantities of pesticides;
• Location of the property including a map with directions;
• Names, addresses and telephone numbers of the owner and key employees;
• Plan of the facility showing pesticides locations, flammable materials, electrical service, water supply, fuel storage tanks, fire hydrants, storm drains, and nearby wetlands, ponds, or streams;
• Location of emergency equipment supplies including breathing equipment and protective equipment;
Copies of the emergency response plan should be located near the entrance to the pesticide facility and with business records. Copies should also be given to the local police department and fire department. Contacts should include the following: fire department; police; spill clean up firm; nearest hospital; pesticide bureau; board of health; owner and or manager of the facility;
The plan should be available in both English and the language or languages understood by workers if this is not English.
Fire Prevention
An automatic smoke detection system or smoke and heat detection system should be installed. The appropriate fire prevention and emergency procedures should be developed in consultation with the local fire department. Suitable methods for extinguishing fires should be installed, such as the appropriate type and number of fire extinguishers. The number and placement of fire extinguishers should conform to the National Fire Protection Association Standard No. 10. All electrical fixtures and appliances should be explosion-proof units approved for use in facilities storing flammable and combustible liquids.
In the event of a fire it is frequently more environmentally sound to allow the fire to burn itself out if it can be contained within the area. This avoids the likelihood of pesticides being released into the ground as a result of water being added. Dry chemical fire suppression systems are superior in chemical storage areas.
Personal Safety
Personal protection equipment such as respirators, chemical resistant (CR) gloves, CR footwear, coveralls with long sleeves, protective eyewear, CR headgear, CR aprons and a first-aid kit should be available immediately outside the storage area. The first-aid kit should include the following items: adhesive strips, tape, ammonia inhalant, eye pads, burn cream, gauze bandages and tweezers. Gloves should be made of rubber, neoprene or other chemical resistant material. It is essential that protective eyewear be worn during mixing/loading. The protective eyewear should consist of safety glasses that provide front, brow and temple protection, goggles or a face shield.
Workers should be instructed in the correct procedure for the removal of contaminated clothing. Eye wash stations or portable eye wash bottles should be easily accessed by each person engaged in the operation and should be capable of flushing eyes for a minimum of fifteen minutes. Drench showers should be located at or near storage and mixing location. Routine wash up facilities, equipped with soap, hand cleanser and single use paper towels should be available near the storage area.
Record Keeping
A daily record of all chemical applications should be located on premises, preferably away from chemical storage areas. All chemical discharges to the environment or spills should be recorded. The records should include chemical or chemicals, the date and time of the incident and the cleanup method.
Accident Response
An absorbent material such as re-usable gelling agents, vermiculite, clay, pet litter, activated charcoal or commercially available spill containment kit should be on hand along with an approved recovery drum and shovel to quickly contain and clean up any small spills.
Security
The chemical storage area should be kept locked when not currently being used by a qualified applicator and the door to the storage area should contain a weather proof sign warning of the existence and danger of pesticides inside. The sign should be visible at a distance of twenty five feet and should read as follows:
DANGER
PESTICIDE STORAGE
AREA and MIXING AREA
ALL UNAUTHORIZED
PERSONS KEEP OUT
KEEP DOORS LOCKED
WHEN NOT IN USE
The sign should be posted in both English and the language or languages understood by workers if this is not English.
While the above has illustrated basic guidelines for the safe storage and mixing of golf turf chemicals they are not intended to be complete or definitive in identifying all hazards associated with your club, preventing workplace accidents, or complying with any safety related, or other, laws or regulations. You are encouraged to alter them to fit the specific hazards or situations of your club and to have your legal counsel review all of your plans and club policies.
Literature sited in the composition of this article:
National Fire Protection Association 434, Code for Storage of Pesticides in Portable Containers
National Fire Protection Association 30, Flammable and Combustible Liquids Code
An H-1group building construction is by definition a high hazard building hallmarked by 4 hour fire resistant exterior walls.
Over Head Door Plan Courtesy Alpine Overhead Door, Inc.
NFPA 101, Section 7-7.3, Other Automatic Extinguishing Equipment
Sump Photo Courtesy of Carbtrol Corporation
NFPA 1600, Standard on Disaster/Emergency Management and Business Continuity Programs
Midwest Plan Service, Pesticide Storage & Mixing Building, 74002, Noyes, R.T. and D.W. Karnmel
Pesticide Storage & Mixing Facilities, Cooperative Extension Service, The University of Georgia, College of Agriculture & Environmental Sciences, Athens, Paul E. Sumner and Michael J. Bader, Extension Engineers
USGA Green Section Record, March / April 1997, Pesticide Storage: One Step Ahead, Gary Bogdanski
Audubon International, Maintenance Facility BMPs-A Self-Assessment Checklist
Best Management Practices for Golf Course Maintenance Departments, May, 1995, Florida Department of Environment, Agricultural Source and Water Well Management Section
The Florida Green, Summer, 1995, Water Quality Management for the Equipment Wash Area, Darren Davis
Equipment Washing Regulations: Michigan Case Study, Michigan Turfgrass, Environmental Stewardship Program, August, 2006
National Fire Protection Association 30, Flammable and Combustible Liquids Code
An H-1group building construction is by definition a high hazard building hallmarked by 4 hour fire resistant exterior walls.
Over Head Door Plan Courtesy Alpine Overhead Door, Inc.
NFPA 101, Section 7-7.3, Other Automatic Extinguishing Equipment
Sump Photo Courtesy of Carbtrol Corporation
NFPA 1600, Standard on Disaster/Emergency Management and Business Continuity Programs
Midwest Plan Service, Pesticide Storage & Mixing Building, 74002, Noyes, R.T. and D.W. Karnmel
Pesticide Storage & Mixing Facilities, Cooperative Extension Service, The University of Georgia, College of Agriculture & Environmental Sciences, Athens, Paul E. Sumner and Michael J. Bader, Extension Engineers
USGA Green Section Record, March / April 1997, Pesticide Storage: One Step Ahead, Gary Bogdanski
Audubon International, Maintenance Facility BMPs-A Self-Assessment Checklist
Best Management Practices for Golf Course Maintenance Departments, May, 1995, Florida Department of Environment, Agricultural Source and Water Well Management Section
The Florida Green, Summer, 1995, Water Quality Management for the Equipment Wash Area, Darren Davis
Equipment Washing Regulations: Michigan Case Study, Michigan Turfgrass, Environmental Stewardship Program, August, 2006
Bollinger, Inc., Bulletin #120, 2006, Golf & Country Club - Pesticide Storage
About the Author
Michael D. Vogt, CGCS, CGIA, is a Golf Facilities Consultant with McMahon Group. McMahon Group is a full-service private club consultancy serving golf and country clubs worldwide. Mr. Vogt can be reached at 800-365-2498 or visit http://www.mcmahongroup.com/ .
About the Author
Michael D. Vogt, CGCS, CGIA, is a Golf Facilities Consultant with McMahon Group. McMahon Group is a full-service private club consultancy serving golf and country clubs worldwide. Mr. Vogt can be reached at 800-365-2498 or visit http://www.mcmahongroup.com/ .
